Koncept štíhlej výroby bol predstavený v ruských podnikoch nie tak dávno v porovnaní so zahraničím, kde sa filozofia Kaizen začala uplatňovať v 50. rokoch. Pred desiatimi rokmi mala iba tretina ruských priemyselných podnikov záujem o optimalizáciu výroby. Teraz budovanie efektívnych výrobných systémov, okrem samostatnej priemyselnej výroby a poradenstva, využívajú nielen veľké, ale aj stredné podniky v mnohých odvetviach hospodárstva.
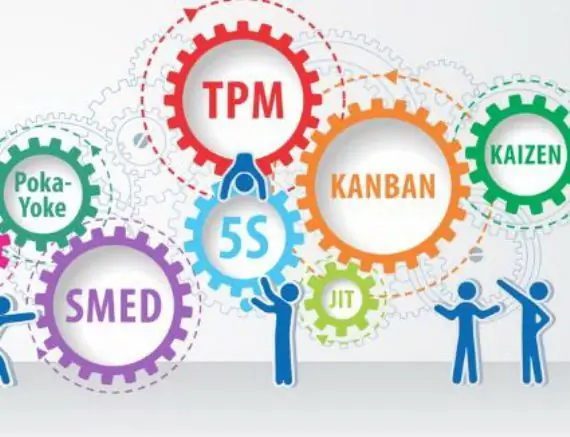
Predchodcami systému štíhlej výroby sú automobiloví giganti Ford a Toyota. Medzi zahraničnými spoločnosťami, ktoré úspešne uplatňujú princípy štíhlej výroby, ako sú Nike, Textron, Parker, Intel, sa za začiatok aktívneho využívania štíhlych technológií v našej krajine považuje rok 2006, keď sa uskutočnilo Prvé ruské štíhle fórum. Priekopníkmi vo vytváraní domácich systémov štíhlej výroby sú naši slávni výrobcovia automobilov - GAZ a KAMAZ. Medzi spoločnosťami využívajúcimi optimalizačné systémy a metódy Lean sú popredné spoločnosti Rusal, Rosatom, Eurochem, TVEL, Sberbank a mnoho ďalších.
Implementácia logistiky štíhlej výroby v ruských podnikoch má štátnu podporu a je regulovaná kľúčovými normami: GOST očíslované R 57522-2017, R 57523-2017, R 57524-2017, ako aj priemyselné odporúčania schválené nariadením ministerstva priemyslu a obchod.
Výraz „Lean manufacturing“alebo LIN je sémantický preklad anglických definícií „lean manufacturing“, „lean production“a prepisu ich skratky LEAN.
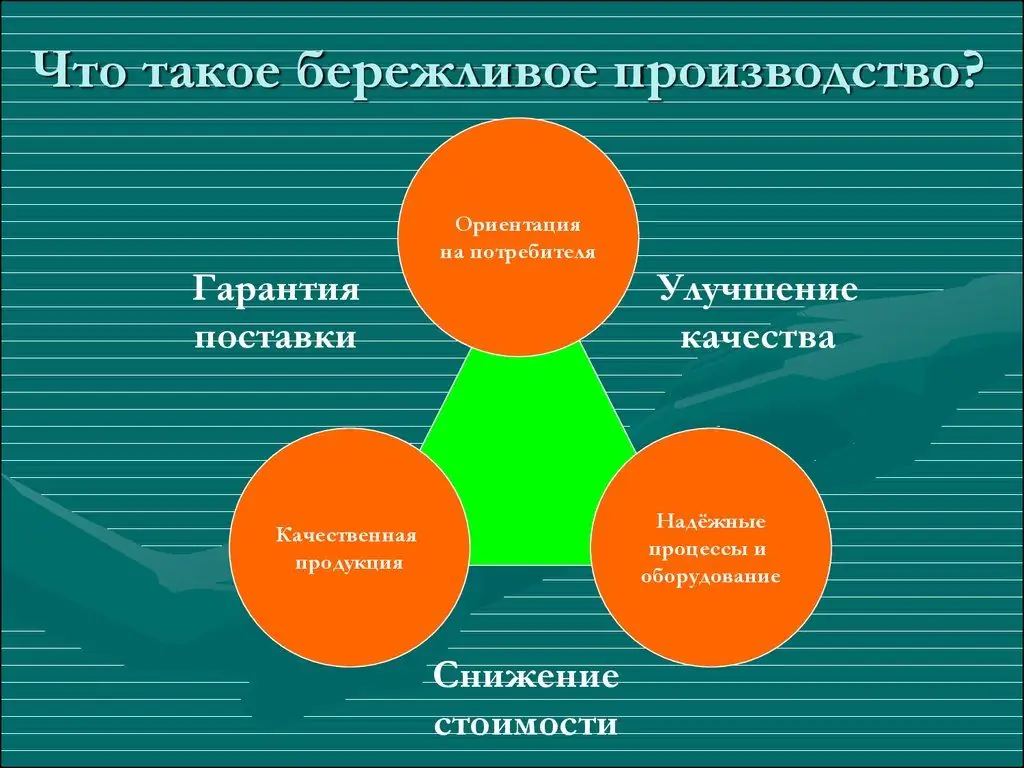
Štíhla výroba sa chápe ako systém riadenia podniku, ktorý vám umožňuje zlepšovať kvalitu práce a zároveň znižovať náklady znižovaním strát.
Anglicko-ruský preklad slova lean je „chudý, štíhly, štíhly“. Aby ste sa stali takými, musíte stratiť prebytočný tuk. Pokiaľ ide o výrobnú sféru, znamená to, že je potrebné zbaviť sa strát, a tým znížiť náklady. Preto sa štíhlej výrobe niekedy hovorí štíhla výroba.
Tri koncepty výroby LIN
Podstatu štíhlej výroby opísal G. Ford, ktorý povedal:.
V systéme štíhlej výroby sú zásadné dva aspekty:
- Do optimalizačných postupov je potrebné zapojiť každého zamestnanca spoločnosti.
- Podnik by sa mal maximálne sústrediť na záujmy spotrebiteľa.
Koncepčne je globálny systém optimalizácie výroby založený na troch princípoch.
- Filozofia Kaizen. Jedná sa o mechanizmy riadenia založené na myšlienke neustáleho zlepšovania kvality a jej prevádzkovej a postupnej implementácie. Stratégia Kaizen je založená na tvrdení, že zdokonaľovanie výrobných procesov nie je nijako obmedzené a každá spoločnosť bez ohľadu na svoju konkurencieschopnosť musí ísť vpred.
- Koncept Six Sigma je založený na skutočnosti, že výrobu môžete riadiť pomocou princípu merateľnosti akýchkoľvek údajov. Keďže sa výrobné procesy merajú, je možné ich monitorovať, a teda zlepšovať, napríklad analýzou kľúčových ukazovateľov výkonu KPI. Koncept je zameraný na to, aby boli všetky výrobné procesy predvídateľné a predvídateľné, vylepšené existujúce a vytvárané nové optimalizačné algoritmy.
- Zvyšovanie efektivity výroby, zlepšovanie kvality vyrábaného produktu pri súčasnom znižovaní nákladov - to sú úlohy systému Lean Manufacturing.
Spoločne tieto tri koncepcie ukazujú, ako postupne a neustále zlepšovať kvalitu výrobných procesov a konečného produktu bez zbytočných nákladov.
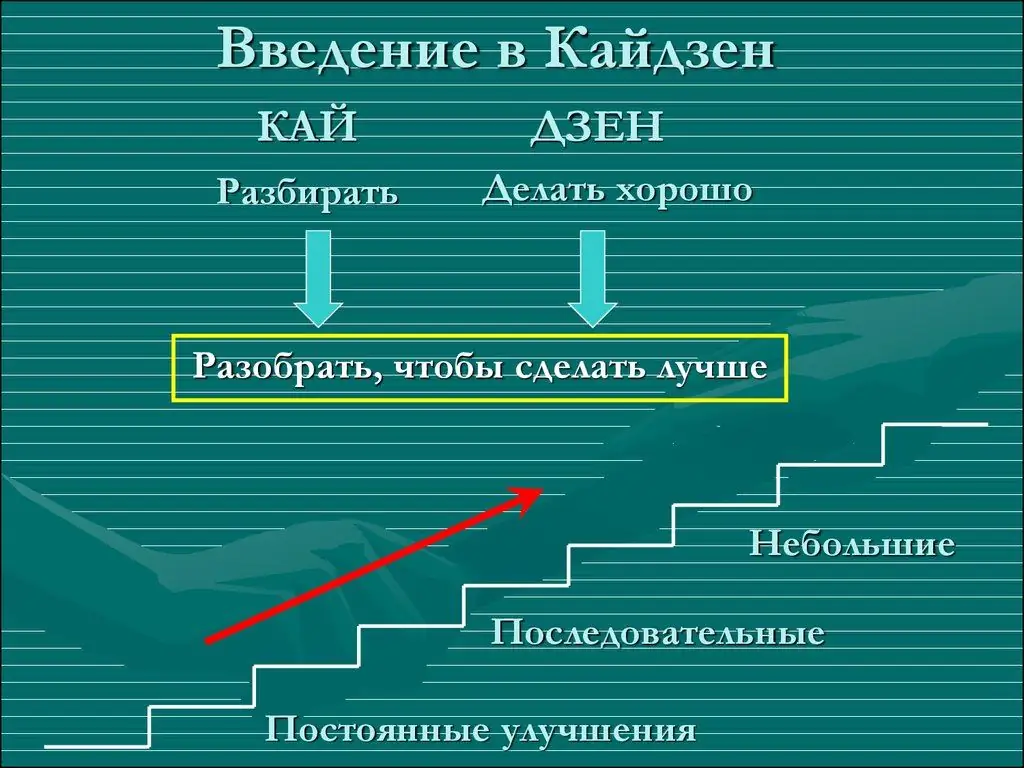
Radikalizmus v riadení výroby bol teda nahradený integrovanou filozofiou, ktorá využíva idealistické princípy liberálnych metód riadenia spoločnosti a implementuje účinné metodiky a nástroje na zlepšenie práce.
Štíhle nástroje
Štíhle technológie sa používajú vo všetkých fázach činnosti podniku - od počiatočného návrhu výrobných procesov až po predaj výrobkov spotrebiteľovi.
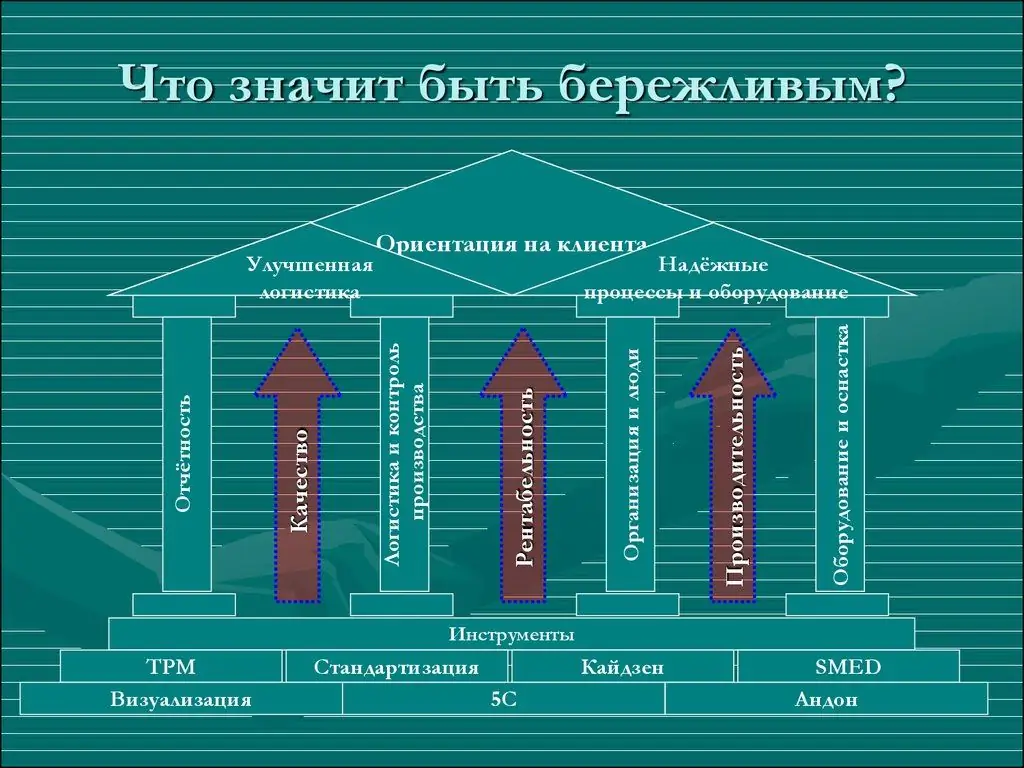
Proces nepretržitej optimalizácie sa vykonáva pomocou nástrojov Lean:
- Celková produktívna údržba zariadení - TPM (Total Productive Maintenance).
- Rýchle prestavenie a prestavba vybavenia „za jednu minútu“a „jedným dotykom“- SMED (výmena matrice za jednu minútu) a OTED (výmena matríc jedným dotykom).
- Organizácia nepretržitého toku materiálu - CANBAN.
- Pull production - pull production.
- Mapovanie hodnotového toku - VSM (Value Stream Mapping).
- Systém riadenia materiálov „just in time“- JIT (Just-In-Time).
- Systém vizuálnej správy a spätnej väzby Andon.
- Štandardizácia pracovného výkonu - štandardné operačné procesy SOP.
- Technológia na vytvorenie efektívneho pracoviska - 5S alebo 5S -CANDO.
- Celkový systém riadenia kvality - TQM (Total Quality Management).
Štíhle nástroje fungujú tak, aby sa zlepšenie kvality práce maximalizovalo a hodnotilo na všetkých stupňoch a úrovniach výroby.